Garantizando Precisión y Seguridad en el Gas y Petróleo Colombiano
Calibración de Equipos de Medida
La calibración es un proceso fundamental para garantizar la precisión y calidad de los instrumentos utilizados en diversas industrias. Este procedimiento consiste en comparar la lectura de un equipo de medición con un estándar de referencia conocido, verificando y ajustando la precisión del equipo para corregir cualquier desviación o error. Durante este proceso, la trazabilidad es crucial: se utilizan estándares de referencia trazables, lo que significa que estos estándares están debidamente calibrados y documentados, permitiendo seguir el rastro de las mediciones hasta normas internacionales reconocidas.
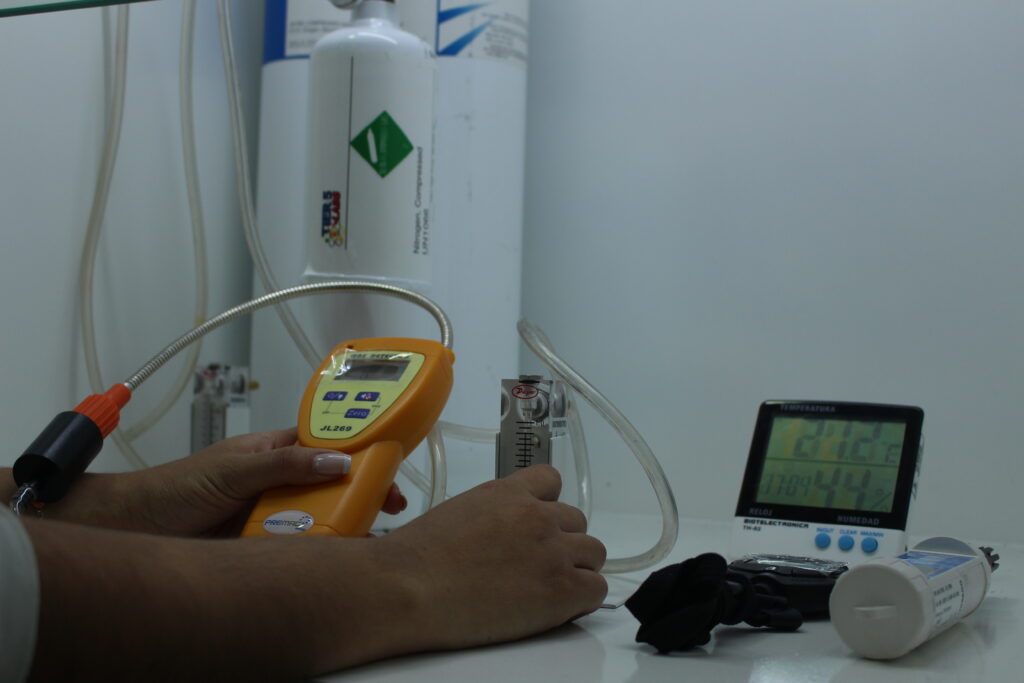
Esto asegura resultados confiables y comparables, esenciales para la toma de decisiones críticas y el cumplimiento de normativas estrictas en sectores como la industria del gas y petróleo. La trazabilidad no solo optimiza el rendimiento de los instrumentos y la integridad de los datos recolectados, sino que también proporciona confianza en las mediciones, asegurando que las acciones se basen en datos precisos y verificables.
Importancia de la Calibración
Es crucial entender por qué es importante calibrar nuestros equipos de manera periódica. Aunque pueda parecer obvio, todos los equipos de medición están sujetos a desviaciones y errores debido al desgaste, envejecimiento o mal uso a lo largo del tiempo. Calibrar regularmente estos equipos es fundamental para detectar y corregir estas desviaciones. Esto no solo asegura resultados confiables y consistentes, sino que también es esencial para tomar decisiones basadas en datos precisos y verificables.
La calibración periódica garantiza que los equipos operen dentro de los márgenes de error aceptables establecidos por normativas y estándares. Esto no solo ayuda a evitar mediciones incorrectas que podrían llevar a decisiones erróneas, sino que también permite identificar cualquier necesidad de ajuste o reparación temprana antes de que se conviertan en problemas mayores. Además, mantener la precisión de los equipos de medición es crucial para cumplir con los requisitos regulatorios y normativos, lo cual puede tener beneficios significativos en términos de eficiencia operativa, reducción de costos y cumplimiento de estándares de calidad.
En resumen, la calibración regular no solo protege la integridad de los datos y la precisión de las mediciones, sino que también optimiza el rendimiento de los equipos a lo largo de su vida útil, asegurando que las operaciones sean seguras, eficientes y confiables.
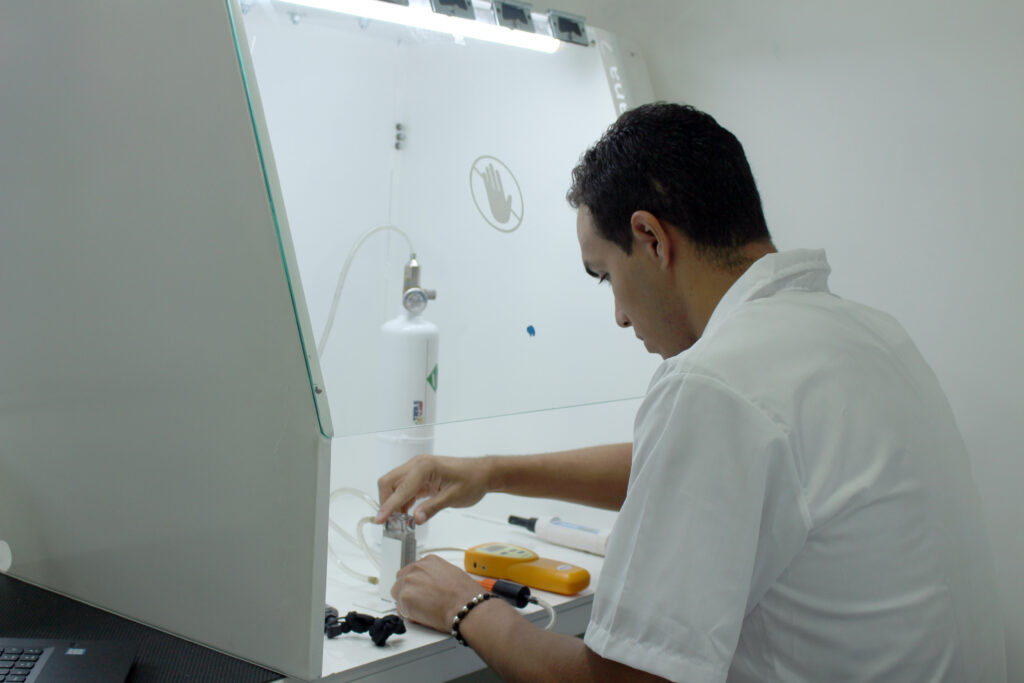
Normas y Regulaciones:
En el contexto colombiano, y en general en el ámbito internacional, las normas específicas para equipos de medición en el sector del gas y el petróleo juegan un papel crucial en garantizar la calidad, precisión y confiabilidad de las mediciones. Además de las normativas locales colombianas que regulan la industria del gas y el petróleo, existen normas internacionales reconocidas que son fundamentales para la gestión de la calidad y la calibración de equipos.
Norma ISO 9000
La norma ISO 9000 es un conjunto de estándares internacionales que establecen directrices para sistemas de gestión de calidad en organizaciones de cualquier tamaño y sector. Aunque la ISO 9000 en sí misma no proporciona requisitos específicos para la calibración de equipos, sirve como marco general para implementar sistemas de gestión de calidad que incluyen procesos como la calibración.
Norma ISO/IEC 17025
La norma ISO/IEC 17025, por otro lado, es específica para laboratorios de ensayo y calibración. Esta norma proporciona los requisitos generales de competencia técnica para laboratorios que realizan calibraciones y ensayos. En el contexto de la calibración de equipos de medición en la industria del gas y el petróleo, la ISO/IEC 17025 establece criterios detallados para la gestión de la calidad, competencia técnica del personal, validación de métodos de calibración, trazabilidad de las mediciones y aseguramiento de la calidad de los resultados.
Normas API (American Petroleum Institute)
El American Petroleum Institute (API) desarrolla y publica normas técnicas específicas para la industria del petróleo y gas. Estas normas abordan diversos aspectos relacionados con la medición, incluyendo la calibración de equipos de medición de flujo, tanques de almacenamiento, y sistemas de control y seguridad. Las normas API son ampliamente reconocidas y utilizadas en la industria para asegurar que las prácticas de medición sean consistentes y confiables.
Normas Colombianas Específicas
En Colombia, las entidades reguladoras como el Ministerio de Minas y Energía y la Comisión de Regulación de Energía y Gas (CREG) emiten normativas específicas que establecen los requisitos técnicos y operativos para la medición y calibración de equipos en la industria del gas y el petróleo.
Estas normas colombianas están diseñadas para asegurar que las empresas cumplan con estándares de calidad y seguridad en todas las etapas de la cadena de suministro de hidrocarburos.
Importancia de Cumplir con las Normas
Cumplir con estas normas específicas no solo garantiza la precisión y confiabilidad de las mediciones, sino que también facilita la comparabilidad de datos entre diferentes operadores y países, promoviendo así una mayor transparencia y eficiencia en el mercado global de energía. Además, el cumplimiento de normativas internacionales como la ISO/IEC 17025 y normas API puede ser un requisito para la certificación y acreditación de laboratorios de calibración, asegurando que los servicios ofrecidos por estos sean reconocidos a nivel internacional.
En conclusión, las normas internacionales y locales específicas para la calibración de equipos en el sector del gas y el petróleo son fundamentales para asegurar la calidad y fiabilidad de las mediciones.
Estas normas proporcionan un marco claro y consistente para la gestión de la calidad, la competencia técnica y la trazabilidad de las mediciones, asegurando que las decisiones basadas en datos sean precisas y efectivas.
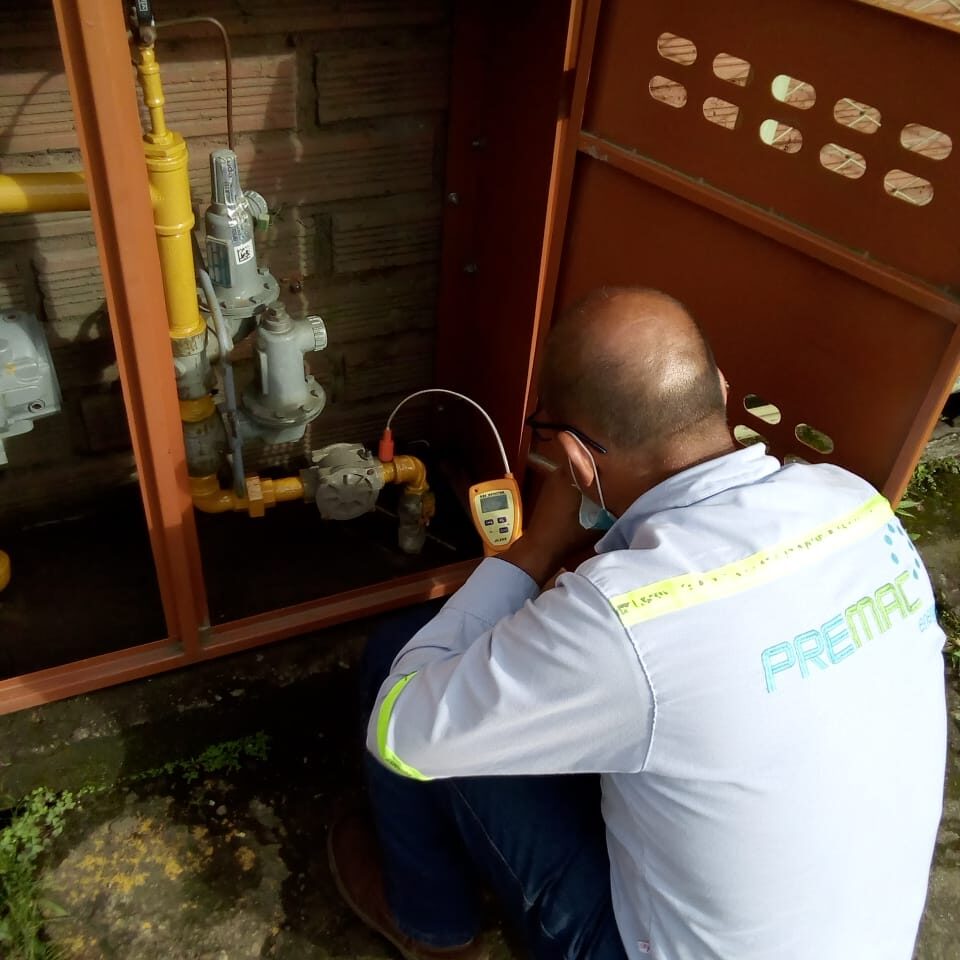
Mantenimiento y Soluciones:
Además de la calibración periódica, es crucial realizar mantenimiento preventivo regularmente para optimizar la vida útil de los equipos de medición en la industria del gas y el petróleo. Este tipo de mantenimiento no solo ayuda a prevenir problemas como desviaciones y errores en las mediciones, sino que también identifica y soluciona posibles fallas antes de que afecten la precisión de los resultados.
El mantenimiento preventivo incluye actividades como inspecciones visuales, limpieza de componentes, ajustes de parámetros operativos y pruebas funcionales. Estas acciones son fundamentales para mantener los equipos en condiciones óptimas de funcionamiento y asegurar su rendimiento confiable a lo largo del tiempo. Además, un programa de mantenimiento preventivo bien diseñado puede reducir el riesgo de tiempos de inactividad no planificados y costosas reparaciones, contribuyendo así a la eficiencia operativa y la rentabilidad de las operaciones en el sector del gas y el petróleo.
Implementar un enfoque proactivo hacia el mantenimiento no solo mejora la confiabilidad de los equipos, sino que también ayuda a cumplir con los estándares regulatorios y normativos, asegurando que las mediciones sean consistentes y precisas. Esto es especialmente crucial en un entorno donde la exactitud de las mediciones tiene un impacto directo en la seguridad operativa, el cumplimiento de normativas ambientales y la eficiencia general de las operaciones.
Instalación y selección de equipos
En cada aplicación, la selección adecuada de equipos es fundamental para cumplir con los requisitos del
proceso, especialmente en líneas de gas natural donde factores como temperatura, presión y caudal son
críticos para la elección del medidor adecuado. Es esencial entender y aplicar correctamente las tablas y
especificaciones proporcionadas por el fabricante o realizar cálculos precisos para determinar el tamaño y tipo de equipo necesario. Aunque las tablas del fabricante simplifican este proceso y ahorran tiempo, es crucial comprender profundamente el funcionamiento de los equipos para garantizar su correcta
instalación y operación.
En cuanto a la instalación, es necesario cumplir con las distancias y disposiciones establecidas por la
normativa correspondiente. Además, se deben aplicar prácticas adecuadas de salud y seguridad laboral
para proteger al personal involucrado y asegurar el cumplimiento de estándares de calidad durante todo el proceso. La organización y la documentación meticulosa de los procedimientos de instalación y
mantenimiento no solo son requisitos administrativos, sino que también son fundamentales para mejorar
la seguridad y la calidad del proceso.
Documentar adecuadamente cada etapa del proceso no solo ayuda a reducir errores humanos y prevenir fallas operativas, sino que también facilita la implementación de mejoras futuras. Esto permite a los equipos técnicos y de gestión comprender mejor el sistema, identificar áreas de mejora y garantizar que las operaciones sean seguras, eficientes y cumplan con todas las normativas pertinentes.
En resumen, seleccionar, instalar y mantener correctamente los equipos en aplicaciones como líneas de
gas natural no solo requiere conocimiento técnico profundo y precisión en los cálculos, sino también un enfoque riguroso en cuanto a normativas, seguridad laboral y documentación. Este enfoque integral no
solo optimiza el rendimiento de los equipos, sino que también asegura la seguridad del personal y la
calidad de las operaciones a lo largo del tiempo.